Use of IoT in Manufacturing: How IoT is Powering the Manufacturing Industry's Evolution
In the realm of manufacturing, the Internet of Things (IoT) has emerged as a catalyst for profound transformation, revolutionizing the way industries operate and opening up new realms of efficiency, productivity, and innovation. By seamlessly connecting machines, devices, and data in a cohesive network, IoT has the potential to optimize processes, enable predictive maintenance, and unlock unprecedented levels of automation, ushering in an era of smart manufacturing. In the article, we will discuss Industrial IoT manufacturing, IoT solutions for manufacturing, will look at challenges and solutions in implementing IoT in the manufacturing industry.
Introduction
The Internet of Things has the potential to bring about transformative changes in the manufacturing industry. Firstly, IoT-enabled sensors and devices can provide real-time data on equipment performance, allowing for predictive maintenance and reducing downtime. Secondly, IoT facilitates seamless communication and coordination between machines and systems, optimizing production processes and improving overall efficiency. Thirdly, IoT enables the collection and analysis of vast amounts of data, leading to valuable insights for process optimization, quality control, and supply chain management. Fourthly, IoT integration allows for enhanced visibility and transparency across the manufacturing ecosystem, enabling better collaboration and coordination among stakeholders. Finally, IoT can enable the development of new business models, such as product-as-a-service, where manufacturers offer their products as a subscription-based service, leading to increased customer satisfaction and recurring revenue streams.
IoT Relevance in the Digital Age
The Internet of Things refers to the network of physical devices, vehicles, appliances, and other objects embedded with sensors, software, and connectivity that enables them to collect and exchange data. It has become increasingly relevant in today's digital age due to its ability to create a seamless and interconnected environment. IoT allows for automation, optimization, and real-time monitoring across various domains, including smart homes, healthcare, manufacturing, transportation, and agriculture. By enabling devices to communicate and share data, IoT offers opportunities for efficiency, improved decision-making, and enhanced user experiences in our increasingly connected world.
With our custom IoT development, you are sure to revolutionize your business and take it to a new level.
Evolution of IoT in Manufacturing
The evolution of IoT in manufacturing has revolutionized the industry by enabling real-time monitoring, predictive maintenance, and optimized production processes. Through interconnected devices and data analytics, manufacturers can achieve greater operational efficiency, reduced downtime, and improved product quality.
Historical perspective on IoT in the manufacturing industry
The evolution of IoT in the manufacturing industry can be traced back to the concept of machine-to-machine communication in the early 20th century, where basic automation systems were implemented to streamline production processes.
In the 1970s, the development of programmable logic controllers (PLCs) revolutionized manufacturing by enabling the integration of sensors and actuators with machines. This laid the foundation for the modern IoT ecosystem in the industry.
With the advent of affordable and powerful computing technologies, such as cloud computing and big data analytics, in the late 20th century, IoT in manufacturing witnessed significant advancements. This allowed for real-time data collection, analysis, and decision-making, leading to improved operational efficiency and productivity.
In recent years, the widespread adoption of wireless connectivity, advancements in sensor technologies, and the emergence of edge computing have further propelled IoT in manufacturing. These developments enable seamless connectivity between machines, devices, and systems, fostering the concept of the Industrial Internet of Things (IIoT).
Today, IoT in manufacturing is transforming the industry with concepts like predictive maintenance, digital twins, and smart factories. It facilitates remote monitoring, predictive analytics, and intelligent automation, empowering manufacturers to optimize production, reduce downtime, enhance quality, and drive innovation.
Current state of IoT in manufacturing
The Internet of Things (IoT) has revolutionized the manufacturing industry by connecting machines, devices, and sensors to enable seamless communication and data exchange. IoT in manufacturing, also known as Industrial IoT (IIoT), has gained significant momentum in recent years, transforming the way factories and production processes operate. Here's a discussion on the current state of IoT in manufacturing.
Adoption and Growth:
IoT adoption in manufacturing is rapidly increasing. According to a survey by IoT Analytics, the global number of IoT-connected devices in the manufacturing sector reached 14.3 billion in 2022, and it is projected to grow another 16% by the end of 2023.
The market size of IoT in manufacturing is expanding as well. Grand View Research predicts that the global IoT market is expected to expand at 23.2% GAGR from 2023 to 2030.
Operational Efficiency:
IoT enables real-time monitoring and data collection, leading to enhanced operational efficiency. Connected sensors and devices gather data on machine performance, energy consumption, inventory levels, and more, allowing manufacturers to optimize processes and make data-driven decisions.
A study by Capgemini found that 76% of manufacturers believe IoT is critical for driving their digital manufacturing initiatives and improving operational efficiency.
Predictive Maintenance:
IoT enables predictive maintenance, a proactive approach to equipment maintenance that uses real-time data to identify potential failures before they occur. This approach helps reduce unplanned downtime, optimize maintenance schedules, and extend equipment lifespan.
Supply Chain Optimization:
IoT plays a crucial role in optimizing supply chain management in manufacturing. By tracking and monitoring assets, inventory, and shipments, IoT enables real-time visibility and efficient inventory management, minimizing stockouts and reducing overall costs.
A recent survey revealed that 28% of manufacturers have implemented IoT solutions to improve supply chain visibility and traceability. Yet, according to the 2023 Survey report by PWC, many challenges still remain, and companies can do more to elevate their supply chains in the digital age.
Growth and future potential of IoT in Manufacturing
The Internet of Things (IoT) is poised to revolutionize the manufacturing industry, with projected growth and immense future potential.IoT enables manufacturers to connect and monitor various devices, machines, and processes, allowing for real-time data collection, analysis, and decision-making. This connectivity enhances operational efficiency, reduces downtime, and enables predictive maintenance, resulting in cost savings and improved productivity. With the integration of IoT, manufacturers can optimize their supply chains by implementing smart inventory management systems and automated replenishment processes. This leads to reduced inventory costs, streamlined logistics, and better demand forecasting, ultimately enhancing customer satisfaction. IoT in manufacturing also enables the implementation of smart factories, where interconnected machines and systems communicate seamlessly. This leads to enhanced automation, increased productivity, and improved quality control. By leveraging IoT technologies, manufacturers can achieve agile and flexible production processes, enabling quick adaptation to changing market demands.
Looking ahead, the future potential of IoT in manufacturing is tremendous. As technology advances, manufacturers can expect further integration of IoT with artificial intelligence, machine learning, and big data analytics. This will enable more sophisticated predictive and prescriptive analytics, intelligent decision-making, and advanced automation, paving the way for Industry 4.0 and the factory of the future.
Understanding the IoT Ecosystem in Manufacturing
The IoT ecosystem in manufacturing refers to the interconnected network of devices, sensors, machines, and software systems that enable data collection, communication, and automation within the manufacturing environment. It encompasses various components such as smart machines, industrial IoT platforms, data analytics tools, and cloud infrastructure, all working together to improve operational efficiency, productivity, and decision-making in manufacturing processes.
Explanation of the IoT ecosystem
The Internet of Things ecosystem refers to the interconnected network of devices, systems, and humans that collaborate to enable the exchange of data and information. At the core of this ecosystem are IoT devices, which can range from sensors and actuators to smart appliances and wearables. These devices are equipped with various sensors and embedded technology that allows them to collect and transmit data.
Connectivity plays a vital role in the IoT ecosystem, as it enables devices to communicate and share data with each other and the cloud. This connectivity can be achieved through various means, such as Wi-Fi, cellular networks, Bluetooth, and even satellite connections.
Once the data is collected from IoT devices, it is often processed and analyzed through data analytics tools and platforms. This allows for meaningful insights to be extracted from the vast amount of data generated by the IoT ecosystem. Data analytics techniques such as machine learning and artificial intelligence can help identify patterns, trends, and anomalies, enabling businesses and individuals to make informed decisions.
Human interaction is an essential aspect of the IoT ecosystem. Users can interact with IoT devices through interfaces such as mobile apps, voice commands, or web portals. They can monitor and control their devices remotely, set preferences, and receive notifications or alerts based on the data collected.
Furthermore, human involvement extends beyond the user level. Developers and engineers are involved in designing and building IoT devices, creating connectivity solutions, and developing data analytics algorithms. Policymakers and regulators also play a role in shaping the IoT ecosystem by establishing standards and regulations to ensure security, privacy, and interoperability.
Overall, the IoT ecosystem encompasses a wide array of interconnected devices, connectivity options, data analytics capabilities, and human interactions, all working together to create intelligent and efficient systems that enhance various aspects of our lives.
Role of technologies in IoT
Technologies like 5G, AI, and Big Data play crucial roles in the development and advancement of the IoT. 5G enables faster and more reliable connectivity, offering higher bandwidth and lower latency, which is essential for IoT devices to communicate and exchange data efficiently.
AI enhances IoT by enabling intelligent decision-making and automation. It enables IoT devices to process and analyze massive amounts of data in real-time, leading to improved efficiency, predictive maintenance, and personalized experiences.
Big Data complements IoT by providing the infrastructure to store, process, and analyze the enormous volume of data generated by IoT devices. It enables the extraction of valuable insights, patterns, and trends that can drive informed decision-making and optimize IoT systems.
The combination of 5G, AI, and Big Data allows for the creation of highly interconnected and intelligent IoT ecosystems. 5G's high-speed connectivity facilitates the seamless integration of numerous IoT devices, while AI and Big Data enable the extraction of meaningful information from the vast amounts of data generated.
Together, these technologies unlock the potential for transformative applications across various industries, such as smart cities, healthcare monitoring, industrial automation, and autonomous vehicles. They enable innovation, efficiency, and improved quality of life by leveraging the power of interconnected devices, intelligent algorithms, and data-driven insights.
Difference between IoT and IIoT (Industrial Internet of Things)
The Internet of Things (IoT) refers to the network of interconnected physical devices, vehicles, appliances, and other objects embedded with sensors, software, and network connectivity that enables them to collect and exchange data. It encompasses various domains such as smart homes, wearable devices, and consumer electronics.
On the other hand, the Industrial Internet of Things (IIoT) specifically focuses on the application of IoT technologies in industrial sectors like manufacturing, energy, transportation, and agriculture. It aims to optimize industrial processes, enhance productivity, and enable data-driven decision-making in industrial settings.
One key difference between IoT and IIoT lies in their respective contexts and target applications. IoT generally caters to consumer-oriented applications and everyday life, while IIoT is centered around industrial automation, operational efficiency, and industrial control systems.
Another distinction is the scale and complexity of the systems involved. IIoT deployments often involve large-scale industrial facilities with intricate networks of interconnected devices, machines, and sensors, demanding robustness, reliability, and security. IoT, in comparison, may encompass a wider range of devices, but they tend to operate on a smaller scale and may prioritize convenience and user experience.
Furthermore, IIoT systems frequently rely on specialized protocols and standards tailored to industrial needs, such as OPC-UA (OPC Unified Architecture) for data exchange in manufacturing environments. IoT, on the other hand, operates on a broader range of protocols and standards to accommodate diverse consumer applications.
In summary, while both IoT and IIoT revolve around connecting devices and collecting data, IIoT specifically addresses the requirements of industrial sectors, emphasizing efficiency, automation, and control, while IoT encompasses a wider range of consumer-oriented applications and contexts.
Impact of IoT on Manufacturing
The advent of IoT (Internet of Things) has significantly transformed the manufacturing industry by enabling real-time monitoring, predictive maintenance, and efficient resource utilization, leading to increased productivity and cost savings. IoT technologies have also facilitated the integration of machines, systems, and processes, fostering greater automation, data-driven decision-making, and improved overall operational efficiency in manufacturing environments.
How IoT is transforming manufacturing processes
The Internet of Things is revolutionizing manufacturing processes by integrating physical devices with Internet connectivity and data analytics. Starting from the design phase, IoT enables manufacturers to create smarter products by embedding sensors in equipment, which gather data on performance and usage patterns. This data is then analyzed to optimize product design and improve overall efficiency.
During production, IoT facilitates real-time monitoring of equipment, allowing manufacturers to detect issues and perform predictive maintenance to prevent breakdowns. Connected devices and machines can communicate with each other, enabling seamless coordination and synchronization on the assembly line. This streamlines production reduces downtime, and enhances productivity.
IoT also plays a crucial role in supply chain management and delivery. Sensors embedded in products or packaging can track their location and condition throughout the logistics process. This enables manufacturers to have real-time visibility into their inventory, optimize transportation routes, and ensure timely delivery. Additionally, IoT enables remote monitoring of goods in transit, allowing for proactive measures to be taken in case of any deviations or damages.
Furthermore, IoT enhances quality control by collecting and analyzing data from connected sensors and devices. Manufacturers can monitor and analyze production data in real-time, identifying deviations and anomalies to ensure consistent quality. This data-driven approach enables continuous improvement and facilitates the implementation of agile manufacturing processes.
Overall, IoT empowers manufacturers to optimize their design, production, and delivery processes by harnessing the power of data and connectivity. By leveraging IoT technologies, manufacturers can achieve increased efficiency, improved product quality, and enhanced supply chain management, ultimately leading to a competitive edge in the rapidly evolving manufacturing landscape.
Benefits of IoT in Manufacturing
IoT in manufacturing offers several significant benefits:
Improved efficiency
IoT enables real-time monitoring and data collection from various manufacturing processes, machinery, and equipment. This allows manufacturers to optimize operations, identify bottlenecks, and make data-driven decisions to enhance efficiency and productivity.
Cost reduction
IoT facilitates predictive maintenance by continuously monitoring equipment health and performance. By detecting potential issues in advance, manufacturers can schedule maintenance activities proactively, reduce downtime, and avoid costly breakdowns.
Mass customization
IoT enables manufacturers to offer personalized products on a large scale. By connecting IoT devices and sensors to production lines, manufacturers can gather customer data, preferences, and feedback in real-time. This information can be used to customize products, adapt manufacturing processes, and deliver tailored solutions.
Shorter time to market
IoT enables seamless integration and communication between different stages of the manufacturing process. Real-time data sharing and collaboration among suppliers, manufacturers, and distributors streamline production, minimize delays, and accelerate time to market for new products.
Enhanced quality control
IoT devices and sensors can monitor quality parameters and collect data throughout the manufacturing process. This allows for continuous quality control and real-time detection of defects or variations. Manufacturers can take immediate corrective actions, ensuring higher product quality and reducing waste or rework.
IoT empowers manufacturers with real-time insights, connectivity, and automation, leading to improved efficiency, reduced costs, mass customization capabilities, faster time to market, and enhanced quality control in the manufacturing industry.
IoT use cases in manufacturing
Here are some IoT use case studies of companies that have successfully implemented the Internet of Things (IoT) in their manufacturing processes. Major IoT in manufacturing examples are:
- General Electric (GE): GE implemented IoT in their manufacturing operations through their "Brilliant Factory" initiative. They integrated sensors and connectivity across their manufacturing processes to collect data in real-time. This helped them optimize operations, reduce downtime, and improve product quality.
- Bosch: Bosch, a leading technology and engineering company, adopted IoT in their manufacturing plants to enhance efficiency and productivity. They utilized IoT devices and sensors to monitor machines, track inventory, and enable predictive maintenance. As a result, they experienced reduced downtime, increased operational visibility, and improved overall equipment effectiveness.
- Siemens: Siemens implemented IoT in their manufacturing plants to create a "Digital Factory." They integrated IoT sensors, data analytics, and machine learning algorithms to optimize production processes, improve quality control, and enable predictive maintenance. This resulted in improved productivity, reduced costs, and enhanced product quality.
- Rolls-Royce: Rolls-Royce, a manufacturer of engines and power systems, incorporated IoT into their operations to enable "intelligent" engines. They used IoT sensors and connectivity to collect real-time data from engines installed in aircraft and ships. This data allowed them to monitor performance, identify maintenance needs, and optimize fuel consumption. It resulted in increased fuel efficiency, reduced maintenance costs, and enhanced reliability.
- Whirlpool: Whirlpool, a leading home appliances manufacturer, implemented IoT in their manufacturing processes to create "smart" appliances. They integrated IoT sensors and connectivity into their products to enable remote monitoring and control. This allowed users to manage their appliances through smartphones and provided Whirlpool with valuable usage data for product improvement and customer support
Role of IoT in Industry 4.0
The Internet of Things plays a crucial role in Industry 4.0, the fourth industrial revolution characterized by the integration of digital technologies into manufacturing processes. IoT enables the interconnectivity of devices, machines, and systems, facilitating real-time data collection and analysis. This connectivity enables improved efficiency, predictive maintenance, and automation, ultimately leading to increased productivity and cost savings in various industries.
Concept of Industry 4.0 and how IoT is a driving force behind it
Industry 4.0 refers to the fourth industrial revolution, characterized by the integration of digital technologies into manufacturing processes to create smart factories. It involves the extensive use of automation, data exchange, and real-time analytics to optimize production and enhance efficiency. IoT (Internet of Things) plays a pivotal role in driving Industry 4.0 by connecting various devices, machines, and sensors within the manufacturing ecosystem. Through IoT, these interconnected devices collect and transmit data, enabling real-time monitoring, predictive maintenance, and intelligent decision-making, ultimately leading to improved productivity, cost reduction, and agile production processes. IoT empowers Industry 4.0 by providing a seamless flow of information, enabling machines to communicate and cooperate with each other, and facilitating the creation of intelligent and interconnected manufacturing systems.
How IoT is enabling smart factories and the digitization of the supply chain
The Internet of Things is playing a significant role in enabling smart factories and digitizing the supply chain. IoT refers to the network of interconnected devices embedded with sensors, software, and connectivity capabilities that enable them to collect and exchange data. By leveraging IoT technologies, manufacturers can create smart factories and transform their supply chains into highly efficient and responsive systems. Here's an explanation of how IoT is enabling these transformations:
Sensor Integration
IoT devices equipped with various sensors can be deployed throughout the factory floor and the supply chain. These sensors can monitor and collect real-time data on factors such as temperature, humidity, pressure, vibration, and machine performance. This data provides valuable insights into the overall health, performance, and utilization of manufacturing equipment, allowing proactive maintenance and optimizing production processes.
Connectivity and Data Exchange
IoT devices in smart factories are connected to each other and to the internet, enabling seamless data exchange. This connectivity facilitates real-time monitoring, control, and coordination of manufacturing operations across different stages of the supply chain. By collecting and analyzing data from multiple sources, manufacturers can gain better visibility into their operations, identify bottlenecks, and make data-driven decisions to improve efficiency and quality.
Predictive Maintenance
IoT-enabled sensors can monitor the condition of machines and equipment in real time. By analyzing the collected data, manufacturers can detect anomalies, predict maintenance needs, and schedule repairs or replacements before failures occur. Predictive maintenance minimizes downtime, reduces costs associated with unexpected breakdowns, and ensures optimal utilization of assets.
Supply Chain Visibility
IoT enables end-to-end visibility in the supply chain by tracking and monitoring products, materials, and assets throughout their journey. RFID tags, GPS trackers, and other IoT devices can be used to capture location, temperature, and other relevant information, providing real-time updates on the status and condition of goods. This visibility allows manufacturers to optimize inventory management, improve logistics, and enhance customer service by providing accurate delivery estimates and handling exceptions more effectively.
Enhanced Automation and Control
IoT enables greater automation and control in manufacturing processes. Smart sensors and actuators can communicate with each other and with central systems, facilitating autonomous decision-making and adaptive control. This automation reduces human intervention, minimizes errors, and increases production efficiency.
Data Analytics and AI
The massive amount of data generated by IoT devices can be analyzed using advanced analytics techniques and artificial intelligence (AI) algorithms. By applying machine learning algorithms to IoT data, manufacturers can gain insights into patterns, identify anomalies, optimize processes, and make predictions. This data-driven approach enables continuous improvement, predictive modeling, and better decision-making across the supply chain.
Challenges and Solutions in Implementing IoT in Manufacturing
Implementing IoT in manufacturing poses several challenges, such as ensuring robust connectivity and interoperability between various IoT devices and systems. Additionally, maintaining the security and privacy of data generated by IoT devices is a critical concern, as it involves sensitive information about the manufacturing processes. To address these challenges, manufacturers need to invest in reliable networking infrastructure, adopt standardized protocols, and implement robust security measures, including encryption and access controls, to safeguard their IoT deployments.
Challenges faced by manufacturers in implementing IoT
Implementing IoT in manufacturing comes with several challenges that manufacturers need to address. Some of the key challenges include:
Data Security and Privacy Issues
IoT implementation involves the collection, transmission, and storage of vast amounts of data. This data often includes sensitive information about products, processes, and even personal data of employees and customers. Ensuring the security of this data throughout the IoT ecosystem is crucial to protect against cyber threats, data breaches, and unauthorized access. Manufacturers need to implement robust security measures such as encryption, authentication, access control, and regular security audits to safeguard IoT systems and data.
Check our article on main IoT security issues and solutions.
Uncertainty about Return on Investment (ROI)
Implementing IoT in manufacturing requires substantial investments in infrastructure, hardware, software, and connectivity. Additionally, there are ongoing costs related to maintenance, data storage, and analytics. Manufacturers may face challenges in quantifying the ROI of their IoT investments, especially in the early stages. It becomes essential to conduct thorough cost-benefit analyses, identify key performance indicators, and set realistic expectations to evaluate the tangible and intangible benefits that IoT can bring to manufacturing processes.
Lack of Qualified Systems and Talent
IoT implementation demands a specialized skill set, including expertise in hardware, connectivity, software development, data analytics, and cybersecurity. Finding and hiring qualified personnel who can design, develop, and maintain IoT systems can be challenging. There may be a shortage of professionals with the necessary IoT skills and experience, leading to increased competition for talent. Manufacturers need to invest in training programs, collaborations with educational institutions, and partnerships with IoT service providers to bridge the skills gap.
Interoperability and Standardization
IoT systems often consist of multiple devices, sensors, platforms, and protocols from various vendors. Ensuring interoperability and seamless integration between these heterogeneous components can be complex. Lack of standardization and compatibility issues can hinder the scalability and efficiency of IoT implementations. Manufacturers should consider adopting industry standards, protocols, and frameworks to enable interoperability, reduce integration challenges, and facilitate the exchange of data between different IoT devices and systems.
Legacy Systems Integration
Many manufacturing facilities already have established legacy systems and equipment that may not be inherently IoT-ready. Integrating IoT technologies with these legacy systems can be a significant challenge. Manufacturers need to assess the compatibility of existing infrastructure, upgrade or retrofit equipment where necessary, and design effective integration strategies to ensure smooth communication and data exchange between legacy systems and new IoT components.
Scalability and Flexibility
As manufacturing operations evolve and expand, IoT implementations need to scale accordingly. This scalability should accommodate an increasing number of connected devices, growing data volumes, and changing business requirements. Manufacturers should design IoT architectures and platforms that are scalable, flexible, and capable of handling future growth and technological advancements without significant disruptions.
Addressing these challenges requires a holistic approach that combines technological solutions, organizational strategies, and collaboration with industry partners. By prioritizing data security, investing in talent development, embracing standards, and ensuring compatibility with legacy systems, manufacturers can overcome the hurdles associated with implementing IoT and unlock the transformative potential of connected manufacturing processes.
Practical solutions and strategies to overcome these challenges
However, there are practical solutions and strategies available to overcome the above-discussed challenges. Let's delve into each challenge and explore potential IoT solutions for manufacturing:
Solutions for Data Security and Privacy Issues:
- Implement robust authentication and access control measures: Manufacturers should employ strong authentication mechanisms such as two-factor authentication and secure access controls to ensure that only authorized personnel can access IoT devices and data.
- Encrypt data in transit and at rest: Manufacturers should employ encryption techniques to protect data while it is being transmitted between devices and when it is stored. This ensures that even if intercepted, the data remains secure.
- Regularly update and patch devices: Keeping IoT devices and software up to date with the latest security patches helps protect against vulnerabilities and exploits.
- Conduct thorough security audits: Regularly assess the security posture of the IoT infrastructure, including penetration testing and vulnerability assessments, to identify and address any potential weaknesses.
Solutions for Uncertainty about Return on Investment (ROI):
- Start with pilot projects: Manufacturers can initiate small-scale IoT projects to demonstrate the potential benefits and ROI. This helps gain confidence and allows for adjustments before scaling up.
- Define clear objectives and metrics: Before implementing IoT, establish specific goals and metrics to measure the impact on key performance indicators (KPIs), such as productivity, quality, and cost savings. This enables a clearer evaluation of the ROI.
- Collaborate with technology providers: Work closely with IoT solution providers to understand the potential benefits and costs associated with implementing their solutions. They can provide insights, case studies, and expertise to help evaluate the ROI.
Solutions for Lack of Qualified Systems:
- Training and upskilling employees: Provide training programs to employees to enhance their skills and knowledge in IoT technologies. This can include workshops, certifications, and specialized courses to develop a qualified workforce capable of managing and maintaining IoT systems.
- Collaborate with external partners: Seek partnerships with IoT solution providers, system integrators, and consultants who have expertise in implementing IoT in manufacturing. They can bridge the skills gap and provide valuable guidance throughout the implementation process.
- Foster internal knowledge sharing: Encourage collaboration and knowledge sharing among employees through internal forums, workshops, and cross-functional teams. This helps build internal expertise and promotes a culture of continuous learning.
Solutions for Other Considerations:
- Prioritize data governance: Establish clear policies and procedures for data governance, including data collection, storage, and sharing. This ensures that data is handled responsibly and in compliance with relevant regulations.
- Address connectivity challenges: Evaluate and address connectivity issues by implementing reliable network infrastructure, such as robust Wi-Fi networks, cellular connectivity, or even edge computing solutions to overcome connectivity limitations.
- Consider hybrid or cloud-based solutions: Adopting hybrid or cloud-based IoT solutions can offload some of the infrastructure and maintenance burdens while providing scalability and flexibility.
Overall, overcoming the challenges of implementing IoT in manufacturing requires a combination of technical measures, strategic planning, and investment in human resources. By adopting these practical solutions and strategies, manufacturers can mitigate risks and unlock the potential benefits of IoT in their operations.
Importance of cybersecurity in the IoT era
In the IoT era, where everyday objects are connected to the internet, the importance of cybersecurity cannot be overstated. With billions of devices exchanging data and controlling critical systems, the vulnerabilities in these interconnected networks pose significant risks. Cybersecurity ensures the protection of sensitive information, safeguards personal privacy and prevents unauthorized access to IoT devices. It is crucial to secure IoT systems to prevent malicious actors from exploiting vulnerabilities and gaining control over connected devices, which could have severe consequences for individuals and organizations. Robust cybersecurity measures, including strong encryption, authentication protocols, and regular security updates, are vital to maintaining the integrity and trustworthiness of IoT networks
Future of IoT in Manufacturing
The future of IoT in manufacturing holds great promise for increased efficiency, productivity, and cost savings. With interconnected devices, real-time data analytics, and predictive maintenance capabilities, manufacturers can optimize their operations, enhance supply chain management, and deliver higher-quality products to meet evolving consumer demands.
You can also check out our article on Top IoT trends to watch in 2023.
Future trends and developments in IoT for manufacturing
The future of IoT in manufacturing will see increased integration and connectivity across the entire production process. Smart factories will leverage IoT technologies to enable seamless communication and coordination between machines, systems, and humans, leading to improved efficiency and productivity.
Edge computing will play a crucial role in IoT for manufacturing, as it allows real-time data processing and analysis at the edge of the network. This reduces latency, minimizes bandwidth usage, and enables faster decision-making, leading to enhanced operational agility and reduced downtime.
The advent of 5G networks will revolutionize the Internet of Things in manufacturing by providing high-speed, low-latency connectivity. This will enable the deployment of large-scale IoT solutions, such as massive sensor networks and autonomous robots, further optimizing processes and enabling predictive maintenance.
Artificial intelligence (AI) and machine learning (ML) will become increasingly integrated with IoT in manufacturing. AI-powered analytics will help manufacturers gain valuable insights from the vast amounts of data generated by IoT devices, enabling predictive maintenance, quality control, and demand forecasting.
Security and data privacy will be critical considerations in the future of IoT for manufacturing. As more devices and systems become interconnected, manufacturers will need robust cybersecurity measures to protect sensitive data and ensure the integrity and availability of their operations. Standards and regulations will evolve to address these concerns and promote secure IoT deployments in the manufacturing sector.
Role of IoT in sustainable and green manufacturing
The Internet of Things plays a crucial role in driving sustainable and green manufacturing practices. Firstly, IoT enables real-time monitoring and data collection throughout the manufacturing process, allowing manufacturers to identify inefficiencies, optimize resource utilization, and minimize waste. This data-driven approach promotes sustainable practices by reducing energy consumption, minimizing material waste, and optimizing production schedules.
Secondly, IoT enables predictive maintenance by monitoring equipment performance and identifying potential failures in advance. This proactive maintenance approach reduces downtime, extends the lifespan of equipment, and minimizes the need for resource-intensive repairs or replacements. By ensuring optimal equipment performance, IoT contributes to energy efficiency and reduces the environmental impact of manufacturing processes.
Thirdly, IoT facilitates supply chain visibility and transparency, enabling manufacturers to make informed decisions about sourcing materials and managing inventories. This visibility helps identify sustainable suppliers and promotes the use of eco-friendly materials and processes throughout the supply chain.
Fourthly, IoT enables intelligent energy management systems that optimize energy consumption in manufacturing facilities. Smart sensors and actuators can automatically adjust lighting, heating, and cooling systems based on occupancy or production demands, leading to energy savings and reduced carbon footprint.
Lastly, IoT enables the development of circular economy models by enabling manufacturers to track and trace products throughout their lifecycles. This allows for effective recycling, reusing, and remanufacturing of products, reducing waste and promoting sustainable consumption patterns.
Potential of IoT in enabling new business models in manufacturing
The potential of IoT in enabling new business models in manufacturing is significant. By integrating IoT devices and sensors into manufacturing processes, companies can gather real-time data on various aspects of their operations, including machine performance, product quality, and supply chain logistics. This data can be leveraged to optimize production efficiency, minimize downtime, and improve overall product quality. Furthermore, IoT enables the implementation of predictive maintenance strategies, allowing companies to proactively identify and address equipment issues before they cause costly disruptions. Ultimately, IoT-powered manufacturing facilitates the transition from traditional linear supply chains to more agile, data-driven ecosystems, opening up opportunities for new business models such as servitization, outcome-based pricing, and customized product offerings.
Conclusion
In conclusion, IoT has emerged as a transformative force in the manufacturing industry, revolutionizing the way businesses operate and boosting productivity. By integrating sensors, devices, and data analytics, IoT enables real-time monitoring, predictive maintenance, and process optimization, leading to improved operational efficiency and reduced downtime. Additionally, IoT empowers manufacturers with valuable insights into their supply chains, enabling better inventory management and streamlined logistics. The seamless connectivity offered by IoT enables greater collaboration between machines, systems, and stakeholders, fostering a more agile and responsive manufacturing ecosystem. As the technology continues to evolve, it is evident that IoT will continue to play a crucial role in shaping the future of the manufacturing industry, driving innovation and unlocking new opportunities for growth.
Besides, by leveraging IoT technologies, manufacturers can enhance efficiency, responsiveness, and customer satisfaction, while also unlocking new business models and opportunities in the rapidly evolving digital landscape.
you may also want to read
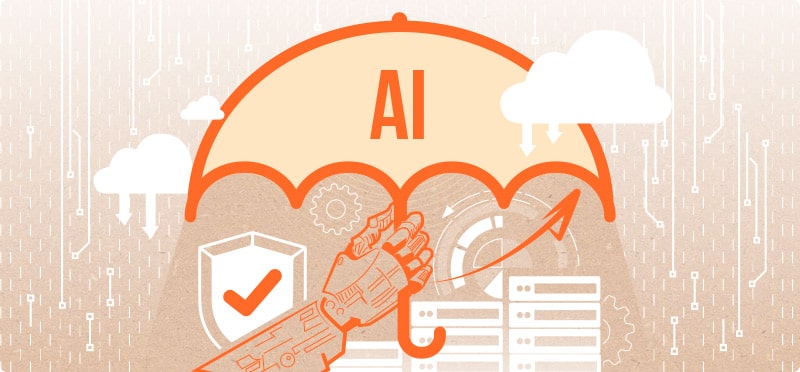
Leveraging Local LLMs and Secure Environments to Protect Sensitive Information
In the rapidly evolving digital landscape, businesses are increasingly adopting Generative AI (GenAI) technologies to stay competitive and innovate. Large...
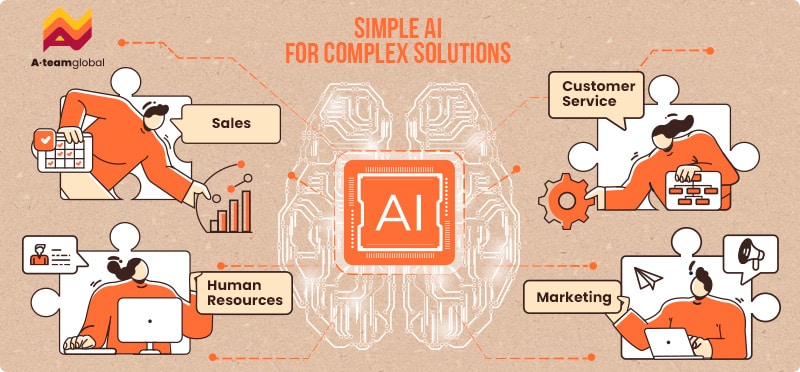
Boost Efficiency Today: Easy AI Integration for Immediate Results
In the past, the idea of integrating artificial intelligence into your business might have felt like venturing into uncharted territory—complex,...
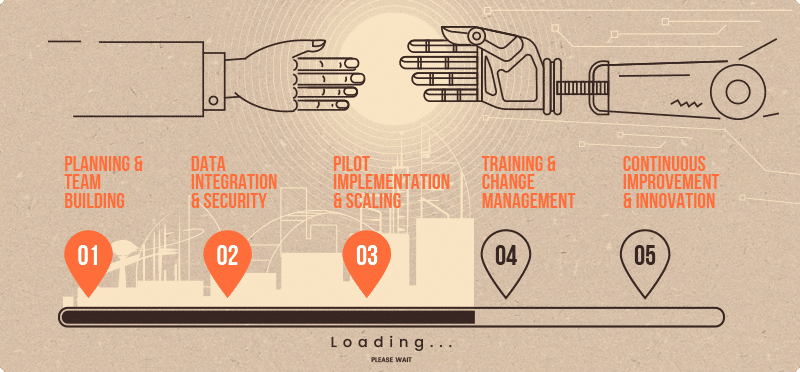
A Roadmap to Gen AI Adoption for Small and Medium Businesses
Unlock new opportunities by integrating Generative AI into your business operations. In today’s fast-paced digital landscape, small and medium businesses...