In the article, we’ll explore the benefits of IoT application in the oil and gas industry, discuss how IoT works in different segments of the oil and gas industry, look at major challenges and considerations as well as future trends.
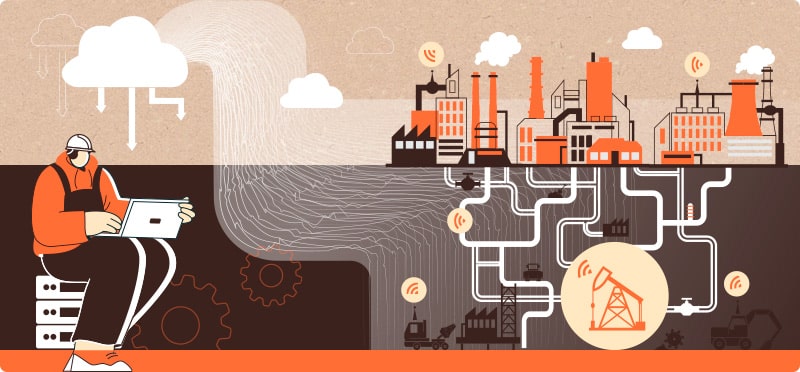
IoT Innovations in Oil and Gas: A Game-Changer for Efficiency and Safety
IoT innovations in the oil and gas industry have revolutionized operations, significantly enhancing efficiency and safety. These advancements enable real-time monitoring of equipment and pipelines, predictive maintenance, and remote control, reducing downtime and minimizing risks. In the article, we’ll look further why IoT has become a game-changer by optimizing resource utilization and ensuring the well-being of personnel in this critical sector.
Introduction
The Internet of Things (IoT) is a concept that refers to the interconnectedness of everyday objects and devices through the internet, allowing them to collect, exchange, and analyze data. IoT devices can range from sensors and cameras to household appliances and industrial machinery, all of which communicate with each other to enhance automation, efficiency, and decision-making.
In recent years, IoT has gained immense importance across various industries, and the oil and gas sector is no exception. IoT is revolutionizing this industry by enabling real-time monitoring, predictive maintenance, and data-driven insights. In oil and gas exploration and production, IoT sensors are deployed on drilling equipment and pipelines to monitor parameters such as pressure, temperature, and flow rates. This data helps optimize operations, reduce downtime, and enhance safety.
Moreover, IoT plays a critical role in refinery operations by ensuring equipment reliability, detecting anomalies, and facilitating remote control. In the transportation and distribution of oil and gas, IoT-enabled tracking and monitoring systems improve supply chain efficiency and reduce the risk of leaks or accidents. Environmental monitoring is also enhanced through IoT, helping the industry minimize its ecological footprint.
The objective of this article is to provide a comprehensive and informative guide on how IoT is revolutionizing the oil and gas industry, IoT applications in the oil and gas industry. It will delve into specific IoT use cases in the oil and gas industry while highlighting the benefits of cost reduction, improved efficiency, and sustainability that IoT brings to this traditionally complex and resource-intensive sector.
With our top-notch IoT product development services, you can expand the potential of your company, increase operational effectiveness, enhance agility, and gain more control over processes and equipment.
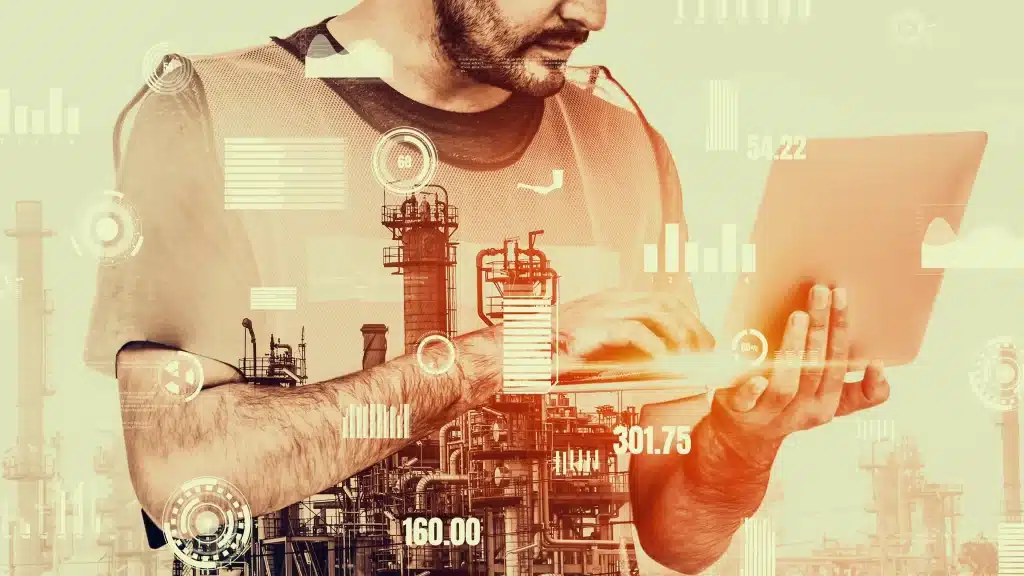
Why IoT in Oil and Gas?
According to Startview Research, the global IoT in oil and gas market is expected to grow from USD 11.34 billion in 2022 to USD 22.24 billion by 2029. IoT solutions can help oil and gas companies better monitor and control their assets. Besides, the oil and gas industry faces numerous challenges that can be effectively addressed through the implementation of Internet of Things (IoT) technologies. IoT offers a range of solutions that can enhance operational efficiency, improve safety, and address environmental concerns. Now let’s look at some key challenges that IoT can address:
Operational Efficiency
Here’s how IoT can improve operational efficiency:
- Asset Monitoring: IoT sensors can monitor the condition and performance of critical equipment such as pumps, compressors, and pipelines. This enables predictive maintenance, reducing downtime and optimizing asset utilization.
- Energy Management: IoT can help in optimizing energy consumption by monitoring and controlling equipment like generators, HVAC systems, and lighting to reduce operational costs.
- Supply Chain Optimization: IoT can provide real-time visibility into the supply chain, including tracking the movement of raw materials, products, and equipment, leading to better logistics and inventory management.
Safety
IoT applications in oil and gas industry can improve worker and environmental safety.
- Worker Safety: IoT can enhance worker safety through wearable devices that monitor vital signs and environmental conditions. In case of emergencies, these devices can trigger alerts or automatically shut down equipment.
- Environmental Safety: Continuous monitoring of emissions, gas leaks, and other potential environmental hazards using IoT sensors can help prevent accidents and reduce the environmental impact of operations.
Environmental Concerns
IoT in oil and gas can successfully address environmental concerns
- Emissions Monitoring: IoT sensors can track emissions and air quality, ensuring compliance with environmental regulations and reducing the industry's carbon footprint.
- Leak Detection: IoT can detect leaks in pipelines and storage tanks promptly, minimizing the risk of oil spills and groundwater contamination.
- Water Management: IoT technologies can optimize water usage in processes like hydraulic fracturing, minimizing water waste and potential environmental damage.
Data Collection and Analytics
Here’s how IoT can also help in data collection and analytics, which is crucial for decision-making in the oil and gas industry.
- Real-time Data: IoT generates vast amounts of real-time data from sensors and devices. This data can be collected and analyzed to gain insights into operations, equipment performance, and environmental conditions.
- Predictive Analytics: IoT data can be used for predictive maintenance, helping to identify equipment issues before they lead to costly breakdowns.
- Operational Optimization: Through data analytics, oil and gas companies can optimize drilling processes, production schedules, and distribution routes to maximize efficiency and reduce costs.
- Environmental Compliance: IoT data can be used to monitor and report on environmental compliance, helping companies avoid fines and maintain their social license to operate.
The use of IoT in oil and gas enables better data collection, real-time monitoring, and data analytics, allowing companies to make informed decisions, improve operational efficiency, enhance safety, and address environmental concerns. By embracing IoT solutions, the industry can not only reduce its environmental footprint but also remain competitive in an evolving energy landscape.
With our IoT-based fleet management systems, you can optimize fleet routes, guarantee that regulatory requirements are met, and lower fuel and maintenance expenses.
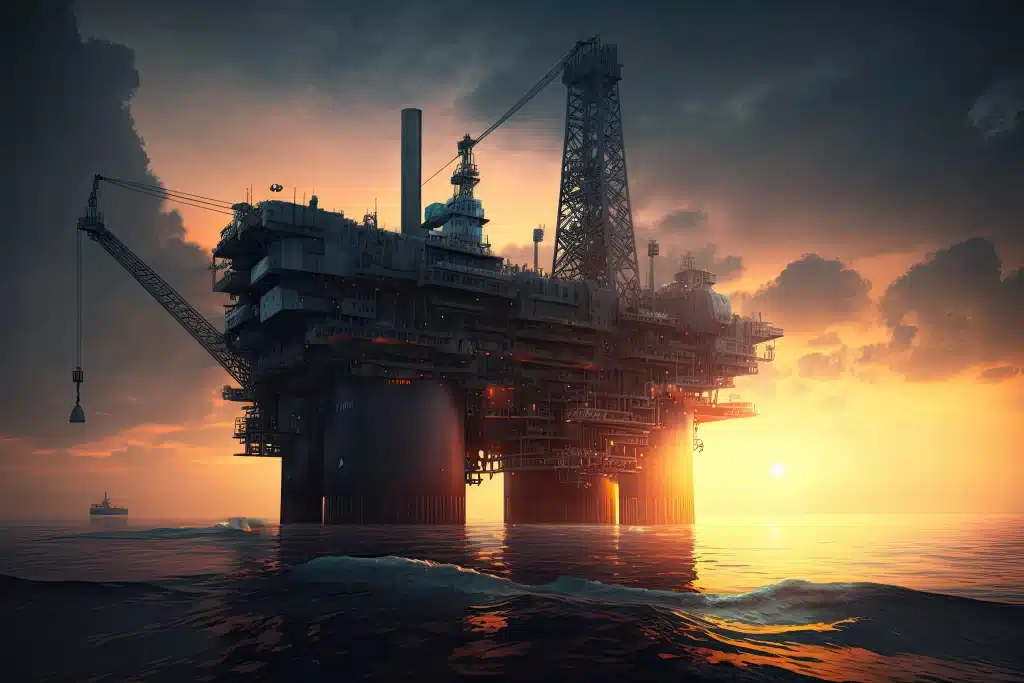
Key Benefits of IoT in Oil and Gas
Here are the major benefits of IoT applications in the oil and gas industry.
Real-time Monitoring
IoT (Internet of Things) technology in the oil and gas industry enables real-time monitoring of equipment and processes. This is achieved through the deployment of various sensors and devices throughout the production and distribution network.
Here's how IoT enables real-time monitoring:
Sensor Integration
IoT devices are equipped with a variety of sensors such as pressure, temperature, humidity, and flow sensors. These sensors continuously collect data from equipment and processes.
Data Transmission
The data collected by sensors is transmitted in real-time to a central control system or a cloud-based platform. This data can be accessed remotely by operators and engineers.
Visualization
The data is then processed and displayed in a user-friendly format, often using dashboards and analytics tools. This allows operators to monitor the status of equipment and processes in real-time.
Alerts and Alarms
IoT systems can be configured to trigger alerts and alarms when predefined thresholds or abnormal conditions are detected. This enables rapid response to issues, preventing equipment failures and safety incidents.
Predictive Maintenance
IoT plays a crucial role in predictive maintenance in the oil and gas industry. Predictive maintenance involves using data from IoT sensors and analytics to predict when equipment is likely to fail so that maintenance can be scheduled proactively.
Here's how IoT enables predictive maintenance:
Data Analytics
IoT systems collect and analyze data from sensors to monitor the condition and performance of equipment. Advanced analytics, including machine learning algorithms, can detect patterns and anomalies in the data.
Predictive Algorithms
By applying predictive algorithms to historical data, IoT systems can forecast when equipment is likely to fail or require maintenance. This allows operators to schedule maintenance activities at optimal times, reducing unplanned downtime.
Condition-Based Monitoring
IoT sensors continuously monitor equipment health, enabling real-time assessment of its condition. This helps in identifying issues early on and prevents costly breakdowns.
Cost Reduction
Predictive maintenance reduces downtime and avoids costly emergency repairs, leading to significant cost savings in terms of maintenance and lost production.
Safety and Hazard Management
IoT enhances safety measures and hazard detection in the oil and gas industry:
Gas Detection
IoT sensors can detect the presence of harmful gases and volatile compounds in real-time. This information helps operators respond quickly to gas leaks and prevent accidents.
Environmental Monitoring
IoT systems can monitor environmental factors such as temperature, humidity, and air quality. This information is crucial for ensuring safe working conditions and environmental compliance.
Asset Tracking
IoT devices can track the location and movement of personnel and equipment in hazardous areas, improving safety and enabling swift response in case of emergencies.
Emergency Alerts
IoT can trigger automatic emergency alerts in the event of a safety hazard or abnormal conditions, allowing for rapid response and evacuation procedures.
Cost Efficiency
IoT contributes to cost efficiency in the oil and gas sector:
Energy Efficiency
Real-time data from IoT sensors can be used to optimize energy consumption in operations, reducing costs and environmental impact.
Resource Optimization
IoT helps in better allocation of resources, such as personnel and equipment, by providing real-time insights into operations.
Asset Utilization
Predictive maintenance and condition monitoring extend the lifespan of equipment, reducing the need for premature replacements and saving capital expenses.
Regulatory Compliance
IoT technology assists in meeting industry regulations and compliance requirements by:
Data Logging and Reporting
IoT systems can automatically record and report data related to operations, safety, and environmental conditions, simplifying compliance documentation.
Continuous Monitoring
Real-time monitoring ensures that operations are in accordance with regulatory standards, helping companies avoid fines and penalties.
Safety Protocol
IoT-enabled safety measures, such as gas detection and emergency alerts, help companies adhere to safety regulations and protect workers and the environment.
You can also check out our article on IoT in the manufacturing industry.
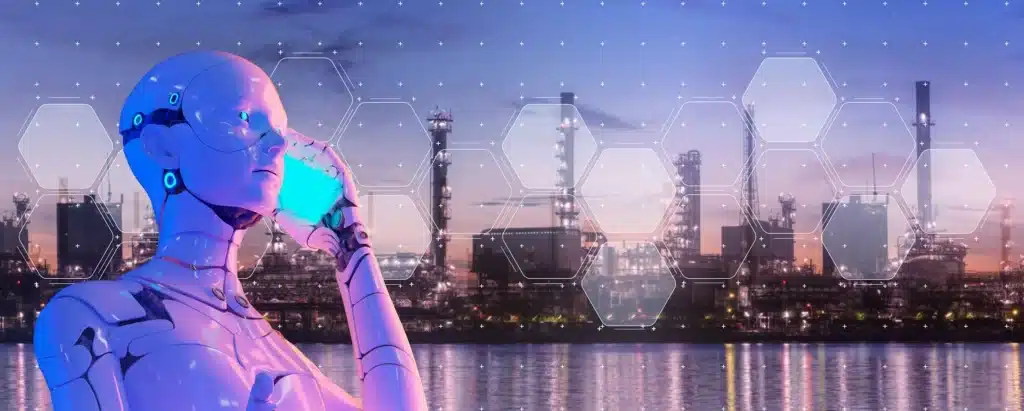
Use of IoT in Different Segments of the Oil and Gas Industry
IoT (Internet of Things) technology plays a crucial role in various segments of the oil and gas industry, enhancing efficiency, safety, and productivity. Here's how IoT in upstream gas and oil industry, midstream, and IoT in downstream oil and gas work:
Upstream: Enhanced Drilling and Extraction Management
- Asset Monitoring: IoT sensors are deployed on drilling rigs, equipment, and wellheads to continuously monitor their condition. This data helps operators schedule maintenance, preventing costly breakdowns.
- Remote Monitoring: IoT enables real-time monitoring of drilling operations from a central control room, allowing for immediate response to any issues or deviations from the plan.
- Data Analytics: IoT devices collect vast amounts of data, which can be analyzed to optimize drilling techniques and predict equipment failures.
- Safety: IoT sensors can detect potentially dangerous conditions, such as gas leaks or pressure anomalies, ensuring the safety of workers.
Midstream: Improved Pipeline and Storage Maintenance
- Pipeline Monitoring: IoT sensors are placed along pipelines to monitor factors like pressure, temperature, and flow rates. This data helps detect leaks, corrosion, or other issues promptly.
- Predictive Maintenance: By analyzing IoT data, midstream companies can predict when maintenance is needed, reducing downtime and minimizing the risk of spills or accidents.
- Environmental Monitoring: IoT can track environmental conditions near pipelines and storage facilities, helping operators respond quickly to any environmental concerns.
- Security: IoT can enhance security by monitoring unauthorized access to critical infrastructure and alerting authorities to potential threats.
Downstream: Optimized Oil and Gas Processing and Distribution
- Refinery Optimization: IoT sensors in refineries monitor equipment performance, enabling operators to fine-tune processes for maximum efficiency and reduced energy consumption.
- Inventory Management: IoT devices can track inventory levels in storage tanks and distribution centers, ensuring that product availability is optimized.
- Supply Chain Efficiency: IoT can be used to monitor the transportation and distribution of oil and gas products, allowing for real-time tracking and route optimization.
- Quality Control: Sensors can continuously monitor product quality, ensuring that it meets industry standards before distribution.
In all segments, data collected by IoT devices is typically sent to centralized platforms for analysis. Advanced analytics, machine learning, and AI algorithms can be applied to this data to gain insights, predict maintenance needs, and make informed decisions.
Case Studies
Here are some real-world examples of companies that have successfully implemented IoT in the oil and gas industry:
Shell's Digital Oilfield
Shell, one of the world's largest energy companies, has been actively incorporating IoT into its operations to enhance efficiency, safety, and productivity in the oil and gas field. Shell's Digital Oilfield initiative involves the deployment of various IoT devices and technologies throughout the entire oilfield lifecycle, from exploration and drilling to production and maintenance. Here are some key aspects of Shell's Digital Oilfield:
- Remote Monitoring: IoT sensors are deployed on drilling rigs, pipelines, and other equipment to collect real-time data on factors such as temperature, pressure, and flow rates. This data is transmitted to central control centers for remote monitoring.
- Predictive Maintenance: IoT data is used to predict equipment failures and schedule maintenance activities before breakdowns occur. This reduces downtime and increases operational efficiency.
- Safety: IoT sensors can monitor for safety hazards, such as gas leaks or equipment malfunctions, and trigger alarms or automatic shut-off systems in case of emergencies.
- Energy Efficiency: IoT technology helps optimize energy consumption by monitoring and controlling equipment remotely, reducing energy waste and operational costs.
- Data Analytics: The vast amount of data generated by IoT sensors is analyzed using advanced analytics to gain insights into oilfield operations and improve decision-making.
Euronav's Fleet Automatic Statistics & Tracking (FAST)
Euronav is a major player in the global shipping industry, and its FAST system is an example of IoT application in the maritime sector, which plays a critical role in transporting oil and gas products. FAST is designed to enhance the management and performance of Euronav's fleet of crude oil tankers. Here's how it works:
- Fleet Monitoring: IoT sensors and devices are installed on Euronav's tanker vessels to collect real-time data on various parameters, including engine performance, fuel consumption, weather conditions, and vessel location.
- Data Transmission: This data is transmitted to onshore data centers via satellite or other communication channels, ensuring that fleet managers can access timely and accurate information about their vessels' status.
- Operational Efficiency: FAST helps optimize route planning, fuel consumption, and maintenance schedules, reducing operational costs and environmental impact.
- Compliance and Safety: IoT technology enables Euronav to monitor compliance with environmental regulations and safety standards, helping to minimize the risk of accidents and environmental incidents.
- Decision Support: Data analytics and visualization tools are used to provide actionable insights to fleet managers, enabling them to make informed decisions and improve overall fleet performance.
These examples demonstrate how leading companies in the oil and gas industry are leveraging IoT technologies to transform their operations, enhance safety, and achieve greater efficiency and sustainability. IoT continues to play a crucial role in reshaping the industry's future.
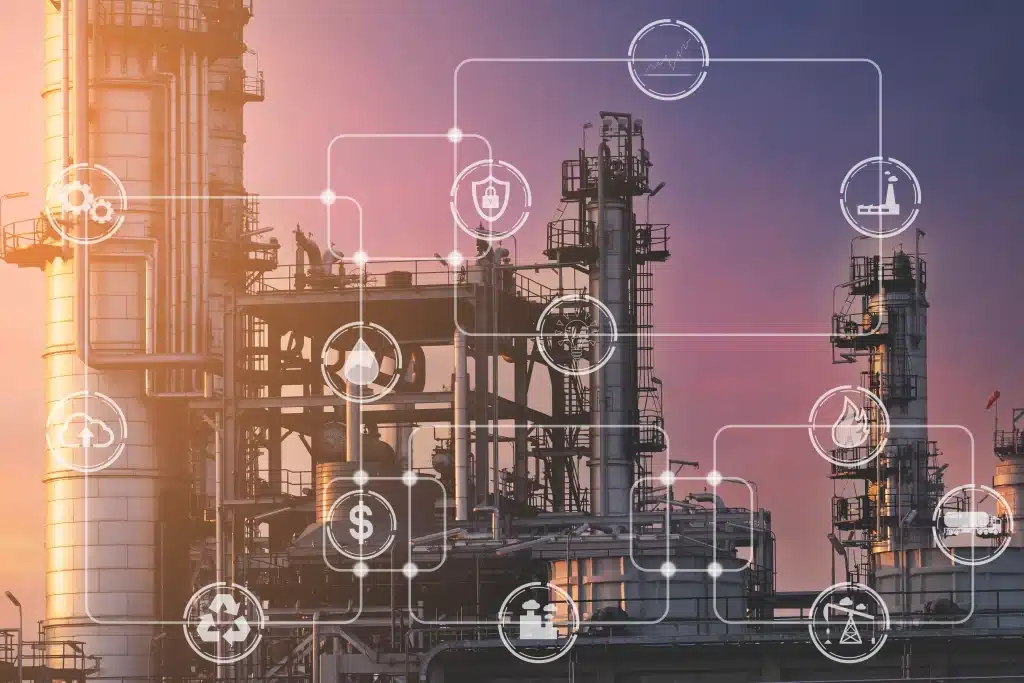
Future Trends
Upcoming IoT (Internet of Things) technologies have the potential to significantly impact various industries, including the oil and gas sector. As we look ahead, several upcoming IoT technologies are poised to further impact this industry in significant ways:
Edge Computing
Edge computing involves processing data closer to the source of data generation rather than relying on centralized cloud servers. In the oil and gas sector, this can lead to faster data analysis and decision-making for critical operations. Edge devices and gateways can collect and analyze data from sensors, reducing latency and enabling real-time monitoring of equipment, pipelines, and reservoirs.
5G Connectivity
The rollout of 5G networks will revolutionize IoT applications in the industry. It will provide high-speed, low-latency connections, making it possible to connect and manage a vast number of devices simultaneously. This will enable more robust remote monitoring and control of drilling operations, refineries, and distribution networks.
Predictive Maintenance
IoT sensors, combined with advanced analytics and machine learning algorithms, can predict equipment failures and optimize maintenance schedules. By continuously monitoring the condition of pumps, compressors, and other machinery, oil and gas companies can reduce downtime, extend the life of assets, and lower operational costs.
Environmental Monitoring
The oil and gas industry faces increasing pressure to minimize its environmental impact. IoT sensors can be used to monitor emissions, water quality, and soil conditions in real time. This data can assist companies in complying with environmental regulations and reducing their carbon footprint.
Cybersecurity Solutions
As IoT adoption increases, so does the vulnerability to cyberattacks. Upcoming IoT technologies will include more advanced cybersecurity measures, such as AI-driven threat detection and encryption protocols, to safeguard critical infrastructure and data.
Energy Efficiency
IoT can play a vital role in optimizing energy consumption within the industry. Smart grids and energy management systems can use IoT data to reduce energy waste and enhance the overall efficiency of operations, resulting in cost savings and reduced environmental impact.
One notable concept in this regard is "Digital Twins." Let's explore this concept and its potential applications in the oil and gas industry:
Digital Twins
A digital twin is a virtual replica or representation of a physical object, system, or process. It uses real-time data from sensors, devices, and other sources to mimic and simulate the behavior, performance, and condition of its physical counterpart.
Potential Impact of Digital Twins in the Oil and Gas Sector:
- Asset Monitoring and Management: Digital twins can be used to create virtual models of oil rigs, pipelines, drilling equipment, and other assets. By continuously monitoring and simulating these assets, operators can optimize maintenance schedules, predict equipment failures, and extend the lifespan of critical infrastructure.
- Predictive Maintenance: In the oil and gas sector, downtime is costly. Digital twins enable predictive maintenance by analyzing data from sensors and historical records to anticipate when equipment or components are likely to fail. This allows for proactive maintenance to prevent costly breakdowns.
- Reservoir Management: In exploration and production, digital twins can simulate subsurface reservoirs. These virtual representations can incorporate geological data, well performance data, and other relevant information to optimize drilling strategies, production rates, and reservoir recovery.
- Safety and Emergency Response: Digital twins can model and simulate various safety scenarios, such as oil spills, fires, and equipment malfunctions. This enables companies to better prepare for emergencies, train personnel, and develop effective response plans.
- Energy Efficiency: Monitoring and simulating energy consumption and production processes can help oil and gas companies identify opportunities for energy efficiency improvements. This can lead to reduced operational costs and a smaller environmental footprint.
Challenges and Considerations
The Internet of Things (IoT) has the potential to revolutionize the oil and gas industry by providing real-time data insights, improving operational efficiency, and reducing costs. However, it also brings forth a set of challenges that need to be addressed to ensure successful implementation. Here are some potential challenges associated with IoT in the oil and gas sector, along with solutions or recommendations:
Data Security and Privacy
- Challenge: IoT devices generate vast amounts of sensitive data, making them potential targets for cyberattacks. Ensuring the security and privacy of this data is a significant concern.
- Solution/Recommendation: Implement robust cybersecurity measures, including encryption, access controls, and regular security audits. Keep software and firmware up to date to patch vulnerabilities. Training employees on cybersecurity best practices is also essential. Additionally, consider using blockchain technology for secure data storage and transactions.
Integration Issues
- Challenge: Many oil and gas companies have legacy systems in place, making it challenging to seamlessly integrate new IoT devices and platforms with existing infrastructure.
- Solution/Recommendation: Conduct a thorough assessment of your current systems and design an integration plan that takes into account legacy systems. Consider using middleware solutions to bridge the gap between old and new technologies. Ensure that IoT devices and platforms are compatible with industry-standard communication protocols.
Data Overload
- Challenge: IoT devices generate massive volumes of data. Handling and processing this data can be overwhelming, leading to inefficiencies.
- Solution/Recommendation: Implement edge computing solutions to preprocess data at the device level, reducing the amount of data sent to central servers. Utilize data analytics and machine learning algorithms to extract actionable insights from the data. Prioritize the collection and transmission of critical data while filtering out non-essential information.
Scalability and Maintenance
- Challenge: As IoT deployments grow, managing and maintaining a large number of devices and sensors can become complex and costly.
- Solution/Recommendation: Develop a scalable architecture from the outset, and choose IoT platforms that can handle growth efficiently. Implement remote monitoring and maintenance tools to reduce on-site visits. Consider predictive maintenance algorithms to proactively address device failures.
Skilled Personnel Shortage
- Challenge: IoT technologies require expertise in various fields, including data science, cybersecurity, and IoT device management. Finding and retaining skilled personnel can be a challenge.
- Solution/Recommendation: Invest in training and development programs for existing employees to build IoT expertise in-house. Collaborate with educational institutions and industry associations to create a pipeline of skilled professionals. Additionally, consider outsourcing specific IoT tasks to experienced service providers when necessary.
Regulatory Compliance
- Challenge: The oil and gas industry is subject to stringent regulations related to safety, environmental impact, and data management. Adhering to these regulations while implementing IoT can be complex.
- Solution/Recommendation: Engage with regulatory bodies and stay informed about evolving regulations. Develop a clear compliance strategy and incorporate it into your IoT implementation plan. Consider using IoT solutions that provide built-in compliance features to simplify reporting and monitoring.
Power and Connectivity in Remote Locations
- Challenge: Many oil and gas operations are located in remote or harsh environments, where power sources and connectivity may be limited.
- Solution/Recommendation: Explore low-power IoT devices and use alternative power sources such as solar or wind energy. Employ satellite or long-range wireless communication technologies to ensure connectivity in remote areas.
You might also want to read more about the use of IoT in logistics and supply chain management.
Conclusion
In conclusion, the integration of Internet of Things (IoT) technology in the oil and gas industry has emerged as a transformative force, revolutionizing operations and enhancing efficiency across the entire value chain. IoT-enabled sensors and devices are facilitating real-time monitoring and data collection, enabling proactive maintenance and reducing downtime. This has not only improved worker safety but has also optimized resource allocation, leading to significant cost savings. The IoT in oil and gas market will continue growing, as such significant factors as the rise in cyberattack risk and the shortage of trained workers in the oil and gas sector continue driving market expansion.
Furthermore, the data-driven insights generated by IoT solutions are driving informed decision-making, allowing companies to optimize production processes and minimize environmental impact. With the adoption of IoT, the industry is becoming more resilient, agile, and responsive to changing market dynamics. However, it's essential for stakeholders to address cybersecurity concerns and invest in robust data management and analytics capabilities to fully harness the potential of IoT in the oil and gas sector. Overall, the future looks promising as IoT continues to drive innovation and sustainability in this critical industry.
you may also want to read
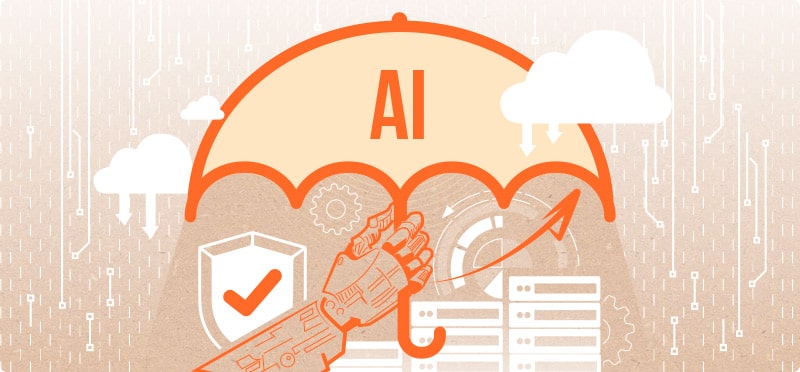
Leveraging Local LLMs and Secure Environments to Protect Sensitive Information
In the rapidly evolving digital landscape, businesses are increasingly adopting Generative AI (GenAI) technologies to stay competitive and innovate. Large...
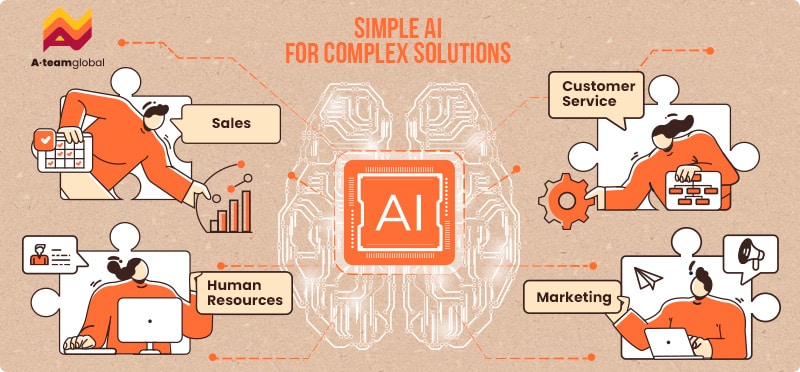
Boost Efficiency Today: Easy AI Integration for Immediate Results
In the past, the idea of integrating artificial intelligence into your business might have felt like venturing into uncharted territory—complex,...
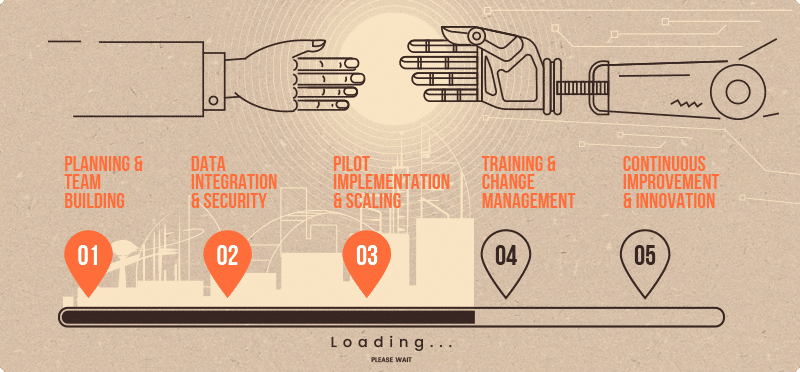
A Roadmap to Gen AI Adoption for Small and Medium Businesses
Unlock new opportunities by integrating Generative AI into your business operations. In today’s fast-paced digital landscape, small and medium businesses...